Call Us Today and Let’s Start Working Together On Your Project.
WHAT IS FUEL POLISHING?
Fuel polishing is the process of removing water, sediments & contaminants from any type of fuel, cleaning the tank in the process, and while not having to dispose of any fuel and not having to take the tank offline.
STATE OF THE ART TECHNOLOGY
Central Waste utilizes state of the art pneumatic fuel polishing and filtering technology to effectively remove water, sediment & other contaminates from all types of fuel. Some of applications for our fuel polishing technology:
Marine– marina storage tanks, gasoline & diesel boats, including US Coast Guard, Navy and PR National Guard facilities.
Critical Power– Hospital and Data Center generator day tanks and large storage tanks.
cRetail Fueling– C-Stores and Truck Stops underground diesel & gasoline storage tanks.
Fleet & Construction Equipment fuel tanks.
Remediation of phase separated ethanol blended fuels.
Aviation Fuel Storage Tanks– Avgas and Jet-A.
- Industrial– Hydraulic and lube oil.
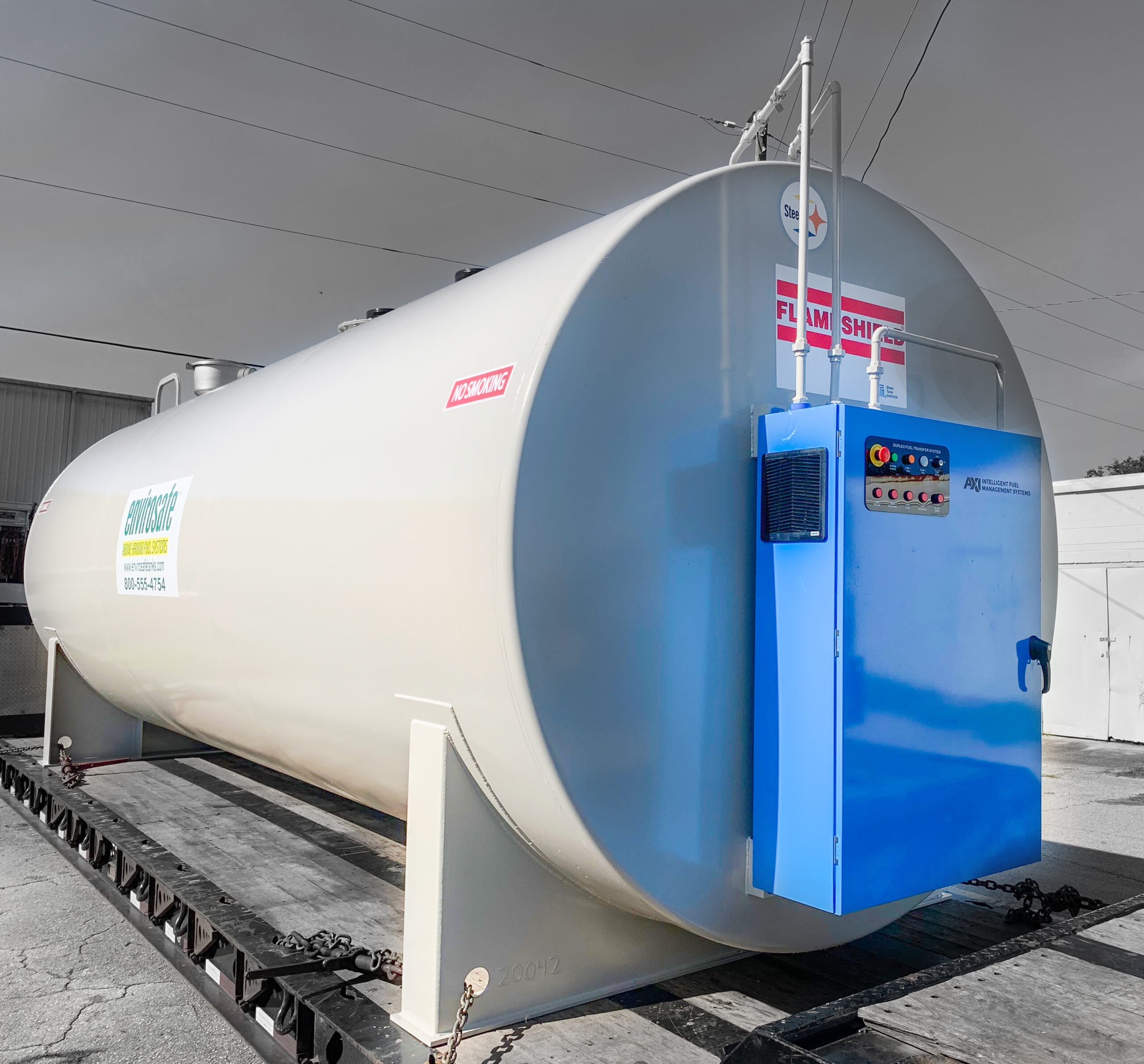
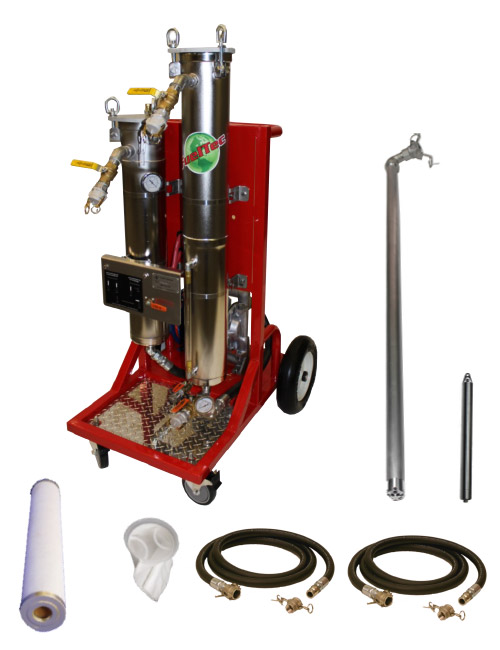
Our 35& 75 GPM pneumatic system is designed to safely purify fluids including gasoline, diesel. hydraulic, motor oils, and jet fuel to meet or exceed the latest engine manufacturer’s cleanliness specifications. Free and emulsified water can be removed to less than 50 PPM. Particulate matter is removed to one micron.
In operation the system pulls fluid from the fuel tank bottom by a vacuum created by the fuel pump. A bag type filter is first to remove sludge and solid contaminates from the tank bottom fluid which may also contain water.
The fuel/water mix leaves the fuel pump under pressure and is forced through a filter/ coalescer where the tiny water droplets are made larger and separate from the fuel. The Teflon separator prevents the water droplets from traveling with the fuel. The water falls to the bottom of the water trap.
A clear sight tube allows you to see the level of the water that has been separated. With the system running, you can open a valve and send the water to a waste container and the clean fuel back to the fuel storage tank. The water level in the sight tube stops rising when all of the water has been vacuumed and separated from the fuel storage tank.
PHASE SEPARATED ETHANOL BLENDED FUELS
Phase Separation happens to ethanol blended gasoline when water is present. When gasoline containing Ethanol comes in contact with water—either liquid or in the form of humidity—the Ethanol will absorb some or all of that water. When it reaches a saturation point, the Ethanol and water will Phase Separate, actually coming out of solution and forming distinct layers on the fuel tank bottom. The result could lower the octane to a point where the engine will not run; or if the alcohol/water mixture is ingested into the engine, sever damage can occur.
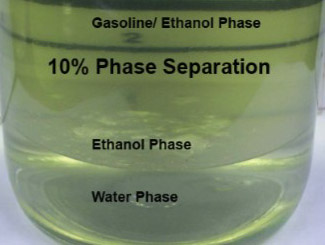
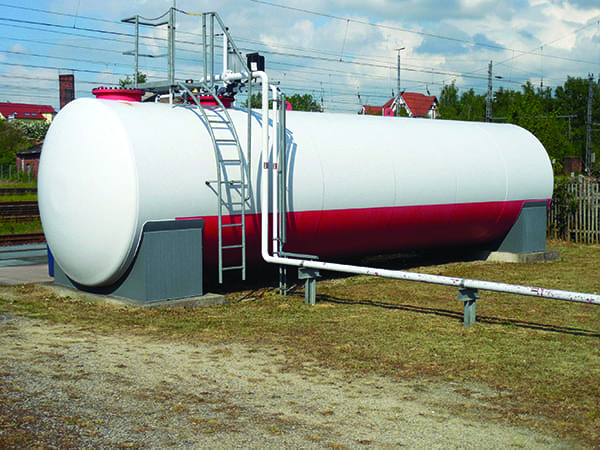
REGULAR MAINTENANCE
Bulk fuel storage tanks should be regularly checked for water and maintained to prevent phase separation. Laboratory tests have proven that our fuel polishing technology will remove the separated phase from the fuel tank in one pass through the system without effecting the clean fuel.
UNDERGROUND TANK CLEANING
“CWS Utilizes State of the Art Jetting Technology to thoroughly and safely clean the inside of underground fuel storage tanks.”
Tank cleaning should be standard practice and is highly recommended by local and federal agencies. Routine tank cleanings are an inexpensive alternative to replacing damaged tanks and equipment. Tank cleanings are not only preventative maintenance but insurance for both the site owner and the land surrounding the tanks.
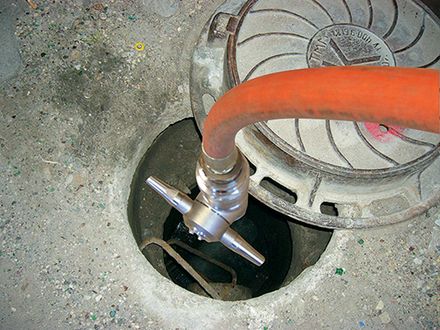